|
Reducing Water Permeance
Reducing Water Permeance
|
|
|
|
|
|
|
|
|
|
|
|
|
|
|
|
|
|
|
|
|
|
|
|
|
|
|
|
|
|
|
|
|
|
|
|
|
|
|
|
|
|
|
|
|
|
|
|
|
|
|
|
|
|
|
|
|
|
|
|
|
|
|
|
|
|
|
|
|
|
WATER SOURCES
CRACKS
DESIGN OF WATER
RESISTANT MASONRY WALLS
WORKMANSHIP
MASONRY
UNITS
MORTAR
COMPATIBILITY OF MASONRY
UNITS AND MORTAR
EVALUATING MASONRY WALLS
AND CHIMNEYS
|
|
|
|
|
|
|
|
|
|
|
|
|
|
|
|
|
|
|
|
|
|
|
|
|
|
|
|
|
|
|
|
|
|
|
|
|
|
|
|
|
|
 |
|
|
|
|
|
|
|
|
|
|
|
|
|
|
|
|
|
|
|
 |
|
|
|
|
|
|
|
|
|
|
|
|
|
|
|
|
|
|
|
|
|
|
|
|
by John Meredith President,
SaverSystems, Inc. |
|
|
|
|
|
|
|
|
|
|
Understanding the causes and
mechanisms of water penetration in masonry will enable technicians to
better diagnose and solve problems before severe damage occurs. Experts
agree that the durability of masonry depends primarily on its resistance
to water penetration. Water damage may include corrosion, deterioration,
dimensional damage, efflorescence, freeze-thaw spalling, staining, damage
to interior finishes, and, ultimately, structural failure. It is well
established that water will penetrate a single wythe masonry wall. Even
masonry walls constructed according to standard ASTM requirements will
permit water penetration through the brick-mortar interface of head and
bed joints. Chimney and wall design, material selection, and quality of
construction are important factors in determining resistance to water
penetration in masonry chimneys or walls. |
|
|
|
|
|
|
|
|
|
|
|
|
|
|
|
|
|
|
|
|
|
|
|
|
|
|
|
|
|
|
|
|
|
|
|
|
|
|
|
|
|
|
|
|
|
|
|
|
|
|
|
|
|
|
|
|
|
|
|
|
|
|
|
|
|
|
|
|
|
|
|
|
|
|
|
|
|
|
|
|
|
|
|
|
|
|
|
|
|
|
|
|
|
|
|
|
|
|
|
|
|
|
|
|
|
|
|
|
|
|
|
|
|
|
|
|
|
|
|
|
|
|
|
The main source of masonry
water intrusion is driving rains, and the level of penetration is affected
by rain quantity and wind pressure. The directional consistency of wind
driven rains can create severe water damage to the affected side of an
exposed masonry surface. Damage from wind driven rain is most severe at
the corners and top of a wall or chimney system because of changes in air
flow patterns at these locations. Since wind speed and rainfall are such
critical factors, a driving rain index for the United States was developed
to illustrate climatic patterns. The driving rain index considers the
average wind speed and rainfall for the country and creates zones on a
scale of 1 to 5, with "1" indicating the least, and "5" the greatest
exposure. Most severe water damage in masonry occurs in ranges 3, 4, and 5
due to frequent freeze-thaw cycles. |
|
|
|
|
Once masonry walls are exposed
to driving rains for several hours they usually reach a saturation point.
Then depending on drying conditions, saturated walls will take from one to
several days to lose most of this water. Trees, plants, and
micro-organisms like algae growing on, or severely shading, masonry
prevent it from drying. With cumulative cycles, a saturation point can be
reached in masonry pores that often leads to leaks or damage to the wall
system. |
|
|
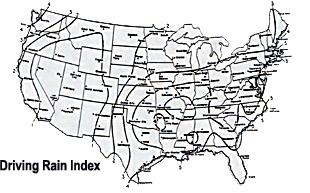 |
|
|
|
|
|
|
|
|
|
Water damage can also be caused
by condensation within the wall system itself. Chimney systems are
especially vulnerable to condensation because water vapor is a large
component of flue gases. Most of the water vapor escapes out the flue, but
some will pass through tile liners and the mortar joints between the
liners.
The greatest exposure to condensation occurs during the
heating season as surface wetting and use of the system produce high
humidity in the air cavities surrounding the liners. When the temperature
of outer masonry walls of a chimney falls below the temperature the air in
the cavity, condensation often occurs on the inside walls. It has been
determined that masonry units can absorb up to .5 lbs of water from
condensation. |
|
|
|
|
|
|
|
|
|
|
|
|
|
|
|
|
|
|
|
|
|
|
|
|
|
|
|
|
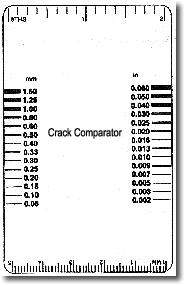 |
|
|
|
|
|
|
|
Although masonry is relatively
dense, it is also a porous material composed of a network of
interconnected pores called capillaries that circulate water by means of
suction. Capillary suction is an important factor for openings smaller
than 0.5mm. Pores in clay brick generally have a diameter of about 0.01mm,
while hairline cracks can range between 0.1mm to 1mm in
width.
Water can enter a wall system through pores and cracks in
the masonry units and the mortar joints, but very often water seeps
through cracks or separations between the masonry and mortar. The water
accumulates until it either penetrates to the interior, drains to
flashings where it is redirected through weep holes, or simply evaporates
through the exterior wall. |
|
|
|
|
|
|
|
|
|
|
|
|
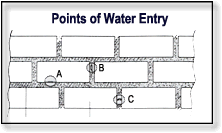 |
|
|
|
|
|
|
|
|
|
|
|
|
|
|
|
|
|
|
|
|
|
|
|
|
|
|
|
|
|
|
|
|
|
|
|
|
|
Field Tip: A crack
comparator for field use can be made by printing this page and photo
copying this article onto transparency film. Keep it at hand to help you
assess the condition of customer's masonry chimney systems. |
|
|
A. Hairline cracks
between mortar and masonry unit. B. Incompletely filled mortar
joints. C. Cracks through mortar.
|
|
|
|
|
|
|
|
|
|
|
|
|
|
|
|
|
|
|
|
|
|
|
|
|
|
|
|
|
|
|
|
|
|
|
|
|
|
|
|
|
|
|
|
|
|
|
|
|
|
|
|
|
|
|
|
|
|
|
|
|
|
|
|
|
|
|
|
|
|
|
|
|
|
|
|
|
|
|
|
|
|
|
|
|
|
|
|
A crack is defined as a break,
fracture, separation, or elongated narrow opening visible on the surface
of a masonry unit or mortar joint, or in the joint between masonry and an
adjacent construction element. Cracks result from strains or stresses
which are greater than the masonry can withstand.
Strains may be
caused by heavy loads, or by volume changes in the masonry materials.
Volume changes may be caused by temperature, moisture, water or salt
crystallization, or corrosion of metals imbedded in the masonry. In
addition, stress cracking may be caused by movements of foundations,
structural frames, wood expansions, vibrations, or fire. Cracks in bricks
that are parallel to the face and to the direction of extrusion are called
laminations are not visible at the surface. All extruded brick laminated
to some extent, and the excessive compressive stress caused by heat,
moisture or freezing may ultimately cause bricks to spall or
de-laminate.
Mortar shrinkage is another common cause of facial
separation cracks in masonry walls. Both the water to cement ratios, and
sand consistency affect the rate of shrinkage. Generally speaking, too
much water or cement in the mortar results in separation cracks.
Weathering and sulfate attack from atmospheric pollutants can also cause
facial separation cracks. However, it has been found that this type of
cracking is most frequently caused by the inadequate tooling of mortar
joints during construction.
Cracks in mortar may also be due to
differences in movement between brick and mortar. For example, if the
thermal expansion of the brick is greater than that of the mortar,
vertical cracks may occur in horizontal bed joints. |
|
|
Design Of Water Resistant Masonry
Walls: |
|
|
|
|
|
|
|
|
|
|
|
|
|
|
|
|
|
|
|
|
|
|
|
|
|
|
|
|
|
|
|
|
|
|
|
|
|
|
|
|
|
|
|
|
|
|
|
|
|
|
|
|
|
|
|
|
|
|
|
|
|
|
|
|
|
|
|
|
|
|
|
|
|
Proper design is critical to
the long-term performance of a wall system. Good design is essential
because it is impossible to keep wind driven rains from penetrating a
single wythe of masonry, regardless of the quality of the materials or
workmanship. |
|
|
|
|
There are two types of wall
design commonly used in commercial construction to control water
penetration. Barrier walls, which were more common prior to 1950, are
typically constructed of 12" of solid masonry. Newer cavity walls are
designed with a back-up wall system. |
|
|
|
|
|
|
|
|
|
|
|
|
|
|
|
|
|
|
|
|
|
|
|
|
|
|
|
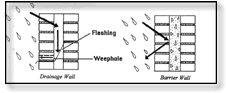 |
|
|
|
|
|
|
This usually consists of a
concrete masonry unit, and more recently, metal studs covered with some
type of sheeting or membrane to prevent water penetration. A minimum 2"
air cavity is recommended between the back-up walls and the exterior brick
facade. Flashing is installed at the base of the cavity to redirect water
outward through weep holes.
Unfortunately, good design components
are not always utilized in residential construction. Residential brick
walls are often laid directly on the foundation with no base flashing or
weep holes. And the lack of proper wall, crown, and flashing design in
masonry chimneys invariably creates water penetration
problems.
|
|
|
|
|
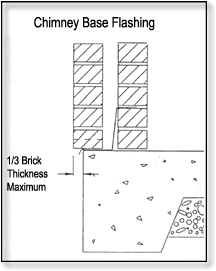 |
|
|
|
|
|
|
|
|
|
|
|
|
|
|
|
|
|
|
|
|
|
|
|
|
|
|
|
|
|
|
|
|
|
|
|
|
|
|
|
|
|
|
|
|
|
|
|
According to the Brick
Institute of America (BIA), base flashing should be used at the joint
between the foundation and the brick work. The flashing should extend
through the brick wythe, turn up behind the exterior of the brick, and be
imbedded into the back-up wall. |
|
|
|
|
|
|
|
|
|
|
|
Above the roof line counter
flashing should be lapped over the base flashing a minimum of 3", extended
through the chimney wall, and turned up into the air space between the
flue tile and the chimney.
|
|
|
|
|
|
|
|
|
|
|
|
|
|
|
|
|
|
|
|
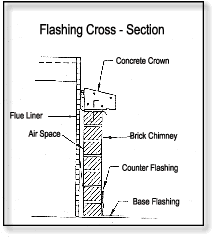 |
|
|
|
|
|
|
|
|
|
|
|
|
|
|
|
|
|
|
|
|
|
|
|
|
|
|
|
|
|
|
|
|
|
|
|
|
|
|
|
|
|
|
|
|
|
|
|
|
|
|
|
|
|
|
|
|
|
|
|
|
|
|
|
|
|
|
|
|
|
|
|
|
|
|
|
|
|
|
|
|
|
After design, workmanship
affects water permeance more than any other factor. The most critical
elements of workmanship to consider in constructing masonry include:
proper mortar materials selection, proportioning/mixing, brick laying and
joint tooling. The selection of compatible brick and mortar is the first
step. Once materials are selected, the bond strength and water resistance
of the wall will further depend on the proportions of the mortar mixture
and the timeliness of the brick laying. All bed and head joints should be
completely filled with mortar. Concave tooling of mortar joints reduces
water permeance, while rough cut, raked, or flat-tooled joints have been
found to increase water permeance.
Separation cracks caused by
improper tooling are common. Research confirms that completely filled
joints, including the vertical head joints, greatly reduces water
permeance. It has also been demonstrated that as the time interval between
spreading mortar and laying brick increases, the water resistance of the
wall system decreases. An interval longer than 1 minute is considered
excessive.
|
|
|
|
|
|
|
|
|
|
|
|
|
|
|
|
|
|
|
|
|
|
|
|
|
|
|
|
|
|
|
|
|
|
|
|
|
|
|
|
|
|
|
|
|
|
|
|
|
|
|
|
|
|
|
|
|
|
|
|
|
|
|
|
|
|
|
|
|
|
|
|
|
|
|
|
|
|
The selection of masonry units
is another important consideration in preventing water penetration.
Although most leaks occur at the mortar joints, a good weathering grade of
brick can help prevent the passage of water. However, masonry units that
are cracked, dirty, or nonuniform in shape and size are more susceptible
to water penetration. In addition, the larger the vertical height of a
masonry unit, the greater the problem of properly filling ti with mortar.
As a result, walls constructed with larger masonry units are usually less
water resistant.
|
|
|
|
|
|
|
|
|
|
|
|
|
|
|
|
|
|
|
|
|
|
|
|
|
|
|
|
|
|
|
|
|
|
|
|
|
|
|
|
|
|
|
|
|
|
|
|
|
|
|
|
|
|
|
|
|
|
|
|
|
|
|
|
|
|
|
|
|
|
|
|
|
|
|
|
|
|
|
It is generally accepted that
masonry. walls constructed with Portland cement lime based mortars are
more water resistant than walls constructed with masonry cement mortars.
Sand gradation in mortar is known to have an effect on the water permeance
of masonry walls; however, masons typically use sand that is locally
available, which varies in grade by region. As sand fineness increases,
more water is needed in the mortar to moisten fine particles. This can
cause excessive shrinkage of the mortar and a loss in bond
strength.
|
|
|
|
|
Compatibility of Masonry Units and
Mortar |
|
|
|
|
|
|
|
|
|
|
|
|
|
|
|
|
|
|
|
|
|
|
|
|
|
|
|
|
|
|
|
|
|
|
|
|
|
|
|
|
|
|
|
|
|
|
|
|
|
|
|
|
|
|
|
|
|
|
|
|
|
|
|
|
|
|
|
|
|
|
|
The compatibility between brick
and mortar is a critical factor in evaluating the water resistance of a
masonry wall. Very often leaks occur in masonry walls that appear to have
few, or no visible cracks. Many leaks in masonry wall systems originate at
the head joints, or vertical joints, because often they are not completely
filled with mortar. |
|
|
|
|
|
|
|
|
|
|
|
|
|
|
|
|
|
|
|
|
|
|
|
|
|
|
|
|
|
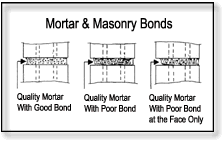 |
|
|
|
|
|
|
|
|
|
|
|
|
|
|
|
|
|
|
|
|
|
|
|
|
|
|
|
|
|
|
|
|
|
|
|
|
Although bed joints, or
horizontal joints, usually are completely filled with mortar, a poor bond
between the brick and mortar can contribute to leakage. The points on a
masonry wall most susceptible to water penetration are at the junctures of
the brick and mortar, referred to as the brick-mortar
interface. |
|
For maximum performance of a
masonry wall, the properties of the mortar should be matched to the
properties of the masonry units. The bond between the brick and mortar is
critical to performance. A poor bond may be obtained by certain
combinations of brick and mortar simply because the two materials are
incompatible, rather than because of a defect in either.
During
moderate construction temperatures of about 80 degrees F, a mortar mix of
1:_:4_ (Portland cement:lime:sand) by volume is recommended for use with
dense brick having water absorption of less than 5 percent. For
medium-absorption brick having absorption between 5 and 10 percent, a
1:1:6 mortar is recommended, and a 1:2:9 mortar is recommended for use
with brick having absorption greater than 10 percent.
|
|
|
|
|
|
|
|
Evaluating Masonry Walls and
Chimneys |
|
|
|
|
|
|
|
|
|
|
|
|
|
|
|
|
|
|
|
|
|
|
|
|
|
|
|
|
|
|
The following list
highlights important considerations for evaluating masonry wall
systems: 1. Pay close attention to wall design and detailing of
copings, sills and wall terminations. 2. Check to see whether base and
counter flashings are missing or improperly installed. 3. Determine
whether weep holes are missing of plugged. 4. Inspect chimney crowns,
which are often poorly designed and improperly constructed. 5. Check
condition of gutters and down spouts to protect walls from excessive
exposure to water.
To prevent water damage, a certain amount of
general maintenance over the life of the structure is usually required.
Sometimes it is necessary to clean or restore masonry before repairs are
begun, but it is important to consider the potential consequences of
various cleaning methods. For example, washing walls with strong acids can
attack and weaken mortar joints leaving them more susceptible to water
penetration. And sandblasting, another common restoration method, has been
found to greatly increase facial separation cracks between brick and
mortar -- which also increases water permeance.
The best choice is
to strike a balance in selecting a method or agent that will allow you to
achieve desired results with the least amount of damage to masonry units
and mortar joints. Proper maintenance and timely repairs are essential for
reducing water permeance and extending the life of masonry walls and
chimneys.
|
|
|
|
|
|
|
|
|
|
|
|
|
|
 |
 |
 |
 |
 |
 |
 |
 |
 |
 |
 |
 |
 |
 |
 |
 |
 |
 |
 |
 |
 |
 |
 |
 |
 |
 |
 |
 |
 |
 |
 |
 |
 |
 |
 |
 |
 |
 |
 |
 |
 |
 |
| Questions and Answers |
©2003, SaverSystems
|
| |